Home
Up
|
Now the head casting has been sorted out, the remaining parts can be made to
complete the basic head. In this state, the head can still not be put to
useful work, as the indexing gear needs to have 24 holes drilled in it.
I'll leave the drilling of the gear until later, rather than rush it for no
good reason.
The spindle
This worries me more than any other part on the head - it has to be a good
fit in the bore of the head casting, without being tight. There's a fair
weight of metal has to come off this bar - a time consuming operation, and machining an
extra 'thou' or two more than planned will render it useless...
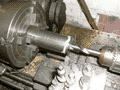 |
14-Mar-2005: Starting off the spindle, the back face has been skimmed.
GHT suggests centre drilling the back face, although I'm drilling it half way
through as the spindle is over 4" in length and drilling in one hit from the
other side will be a bit of a chore. |
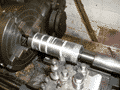 |
With a centre for support, the spindle is being roughed down to 1.125"
diameter. I did spend some time recently truing up the lathe bed, and
correcting the tailstock offset which seems to have paid off.
Checking in five places along the bar with the digi-caliper
gives identical readings of 1.1245". This is, of course, pushing the
repeatability and accuracy of the caliper somewhat. |
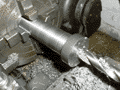 |
Turned round and re-centred in the 4 jaw chuck, it's being drilled through
from the front. The job is made a lot easier by previously drilling from the
back. This is about as much as I can do for now as I don't have
a boring bar long enough to do the length of the spindle... |
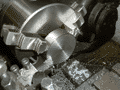 |
17-Mar-2005: The thrust nuts are being made while I'm waiting for
some extra tooling to turn up. Both faces of the nut have to be parallel, this being
especially important for the nut with the larger hole which takes up any
axial play in the spindle. One end of the bar section is being faced. |
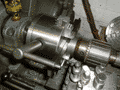 |
The bar is turned round, and parallels are used to get the back square
to the axis of the lathe, the chuck is giving a 'push' to the bar to ensure
it's tight against the parallels. This method did not prove satisfactory,
so I used a couple of smaller parallels 'end on' which gave much better
results. |
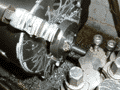 |
Once the nut blank is squared up, it's simply a case of trimming the thickness
and boring/threading. |
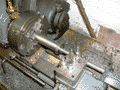 |
18-Mar-2005: The blacksmiths drills and 3/4" machine reamer have arrived,
the homemade long 1/2" boring bar has been made. Just machining the
spindle out to 0.746", a task which took a couple of hours as the extra
length boring bar can only take 0.005" off at a time without 'squeaking'. |
 |
Finishing to 0.751" with the machine reamer, quite impressed with this -
the shank looks like it's forged/rolled, the first 3/4" is
definitely solid carbide (and suprisingly it's British). A bargain at £16
from Tracy Tools.
If you need reamers, taps, or drills give them a shout. |
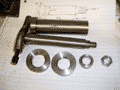 |
20-Mar-2005: The kit contains material to make the mandrel on
which the spindle is mounted for final turning. This ensures that the
centres are concentric on the spindle. |
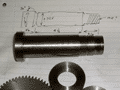 |
The almost finished spindle - a keyway will need to be cut in it for
positively locating the large gear, and the nuts need to be tapped for
clamping screws. |
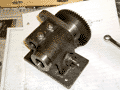 |
Temporarily assembled, it's all starting to look like a dividing head.
Everything fits well, which is something of a relief... |
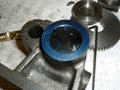 |
24-Mar-2005: The front face has been blued up, and not a trace of
dye being scraped off due to the spindle riding on the chamfer.
The spindle was undercut slightly and the front face scraped in, followed
by the back face. |
Other items
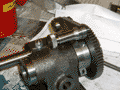 |
25-Mar-2005: These were fairly uneventful, no problems encountered.
Just need a ball handle now, and this section is finished - the 24 holes in the gear
and the three holes in the spindle come later when more of the dividing head
has been built. |
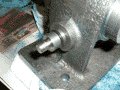 |
27-Mar-2005: Here's a small modification. Any excess of oil
in the dividing head will migrate to the well in which the spindle
clamp lives. This will eventually drip out of the hole in the side
and look untidy. A groove has been machined for an 'O' ring, which
serves the dual purpose of keeping oil in, and adding a little friction to
prevent the lever from flapping around. |
|