Home
Up
|
There are plenty of accessories that can be made for the VDH, and some
are required to make the head in the first place. I've listed them
here in the order they were made.
LA faceplate and Myford spindle adapter
A light alloy faceplate - this is an unmachined casting which can be obtained
from Hemingway, and makes the job of drilling the plates much easier. A
steel section is glued into the front of the faceplate to allow work to be bolted
through the centre of the plate.
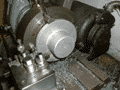 |
07-Apr-2005: The casting being trued up in the four jaw chuck.
It's in the chuck back to front, as this will allow the thread and recess for
the register to be machined. |
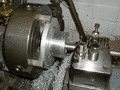 |
The back of the plate and outside of the boss have been machined, and a
boring bar run through to increase the diameter to a size suitable for cutting
the 1-1/8" x 12TPI thread. |
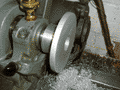 |
After threading and finishing the recess to size, the faceplate can be
removed from the chuck and screwed onto the lathe spindle. |
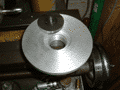 |
A recess has been machined in the front of the faceplate to accept a steel
disc. The disc has been turned down to 1.6" diameter from a small section
of 1/4" steel plate - this will now be pressed into the recess and secured
with Araldite. |
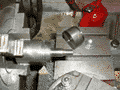 |
14-May-2005: This is the retainer which will pass through the centre
of the plate and hold it onto the faceplate. Before parting this off... |
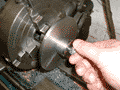 |
it can be used in situ with a suitable spacer to trim up the plates to the same
size. The edge of the plates can be chamfered at this point too. |
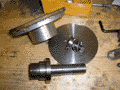 |
Pictured here the Myford spindle adapter with the LA faceplate and the
plate retainer. The LA faceplate has had three holes drilled in it to
take 1/2" x No.6 screws to hold the plywood sheet on. Nothing special
about the Myford spindle other than it was made from two sections of bar
glued together to cut down the machining time. |
Headstock dividing attachment
A very simple but effective attachment that allows headstock dividing to be
carried out. The gadget consists of three main parts - a 1/2" shaft with
a 2MT end, a 3/4" sleeve with a chamfer on the end to fit the spindle, and
a support bracket.
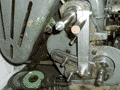 |
18-May-2005: View of the attachment before the dividing head is
coupled up. The base of the support bracket is held to the quadrant using
the pin from the Myford catchplate (5/8" diameter). The sleeve could
do with three 2BA grub screws near the lathe end to prevent eny slip. |
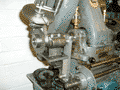 |
With the Versatile Dividing Head attached. The assembly is fairly
solid, and works well. The only downside is the spindle locking lever
is on the opposite side, although access is very good so it doesn't cause
any major problems. |
2MT sleeve
A simple sleeve that plugs into the 3/4" bore and accepts 2MT tooling.
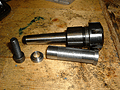 |
28-Dec-2006: The sleeve pictured here with a 2MT / ER25 collet chuck. I'm standardising on
ER25, so the sleeve (and collet chuck) allow me to hold circular items up to 16mm in diameter. The sleeves described
by GHT are useful in that they allow materials through the bore, but this setup here will probably cover 99% of what
I need to do. |
|