Home
Up
|
I've had the mini mill for around a year now and all the end mills
and other tools have always been held in the jacobs chuck. This is clearly not the way to
do it, and has led to some "interesting" moments. I don't want to take any other projects forward,
those than involve milling anyway, until this one is completed.
Armed with a sketch of what I think a tool holder should look like, construction has started.
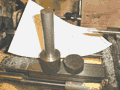 |
21-Apr-2003: The materials have been prepared - as the holder has a
thick end and a thin end, it created the problem of having to remove a lot of steel to get the correct shape.
This has been avoided by glueing 1" diameter and 2" diameter steel bars together using epoxy adhesive and an interference fit of 0.05mm (0.002").
The other 2" diameter offcut will end up being the screwed retaining ring.
|
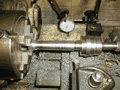 |
The external turning has been finished, including the MT3
morse taper and the M42x2.0 thread for the retaining ring on the end.
I've deviated from the sketch a little bit and left a ring on the thick end to
allow for knurling.
|
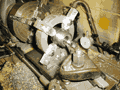 |
22-Apr-2003: The new fixed steady is earning its stripes
allowing the 25mm hole to be bored in the end. This is the final bit, a 15 degree taper
at the end of the bore. All this part needs now is the other end drilling and tapping
for the M12 drawbar that comes with the mini mill, and some knurling if the diameter will
fit within the capacity of the knurling tool I have. The boring tool shown is a simple "D bit", Gingery style.
|
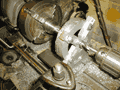 |
27-Apr-2003: Flipped round, the thin end is now
being bored to take the M12 tap for the drawbar. Aside from the knurling and
checking the accuracy of the Morse taper, the main body of the tool is complete.
|
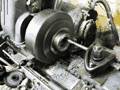 |
Last part, the retaining ring which will screw onto
the M42x2 thread of the toolholder and keep the collet in. This is the retaining
ring being bored prior to internal threading. After the picture
was taken, the internal threading tool disintegrated due to careless use.
More next weekend...
|
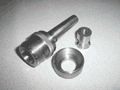 |
02-May-2003: New threading tools have arrived so the final
details have been finished. The collet shown is 1/2" (there is only one right now),
all the parts have been cleaned with Brillo pads ready for oxide coating.
|
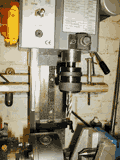 |
Oxide blacked and fitted to the mini mill. Seen here
holding a 7/16" endmill (1/2" shank). Need some more collets now... I
know that MT3 collet systems can be bought from a number of sources, but it was interesting to try and make
one and practice some accurate machining.
|
|